The fifth rotation of the trainee program is now complete. During this period, I have been at Thomas Betong, Sweden’s Precast. I have worked not only in Gothenburg but also at the office in Stockholm and the Precast Concrete plants in Sollebrunn and Heby. This rotation has been very broad, and I have had the opportunity to:
- Work with the technical sales team, sending quotes to customers.
- Gain insight into the design, dimensioning, and drawing processes of precast concrete elements.
- Understand the daily work of a project manager before and during the construction phase.
- Get hands-on experience in building concrete elements.
- Observe the assembly of precast elements at the construction site.
The period at the Precast Concrete division has been spread out over the year and during that time I have got to meet a lot of the amazing colleagues in Team Thomas. For you to better follow along I will not present the period in chronological order, instead following the divisions well-structured work process from quote to delivery.
The work process starts with the technical sales team, which participates in the customers’ procurement phase of choosing precast concrete elements. The tasks during this phase can be summarized as sending quotes, contract negotiations, and finalizing agreements.
During this period, I worked together with the technical sales team and gained insight into the work behind sending quotes. I thought it was very challenging to make a quote because of the scope of the request of proposal. Sture Svahn, Technical Sales in Stockholm, explained the different steps and how to approach the process. Together, we created an actual quote and sent it to the customer, which was fun!
Once the agreements are finalized, the sales team hands over the baton to the project managers. The project managers then take over to ensure the successful execution of the project. Prior manufacturing and delivery of the precast concrete elements, the project manager coordinates the design phase of the project. The design phase quickly transitions to the construction and delivery of the precast concrete elements to the customer.
The tasks of the project manager are very varied and involve a lot of coordination, both before and during the project. This includes contact with the customer and extensive planning to ensure the construction and delivery of the precast elements so that they arrive at the construction site on the customer’s request. Nina Torehov and Rebecka Johansson, Project managers at Ringön, explained the process from quote to delivery and we got the opportunity to gain insight in how delivery plans are made, to participate in project start meetings, coordination meetings etc. It’s impressive how many tasks a project manager has to juggle and the knowledge they need to coordinate everything. Their ability to manage multiple things at once and keep everything on track is impressive.
The coordination of the drawing and dimensioning is done and led by Thomas Betong’s highly skilled design team of structural engineers and project managers. Anette Jansson, Azmi Al-Eesa, and Tobias Nannesson, structural engineers at Ringön, explained their daily work, their roles, and the challenges they face as structural engineers. During the three-week period, I worked on a project modeling prestressed filigree floor slab. It was a challenging project, and it was very helpful to have such a highly skilled design team in-house to ask for help.
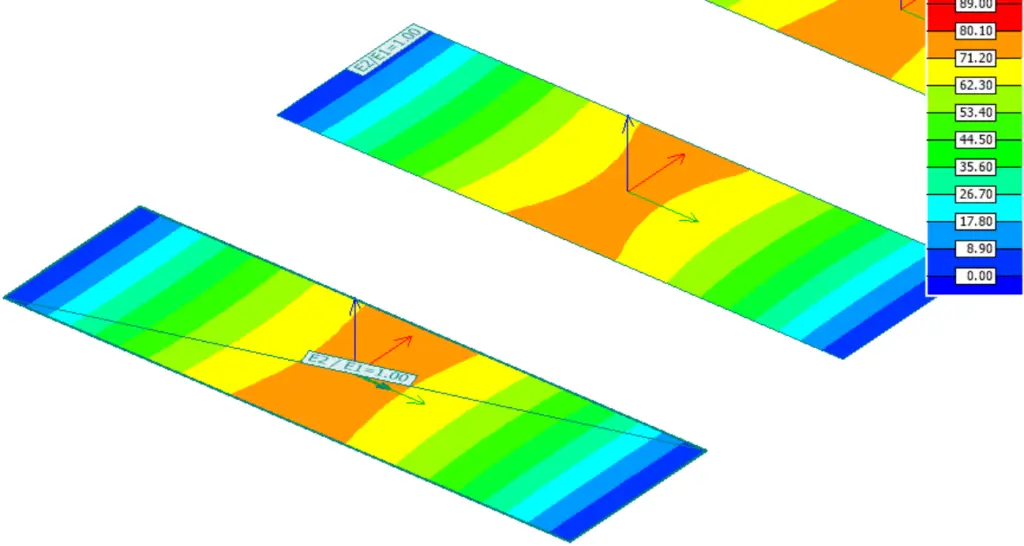
After the dimensioning and drawings are done, the precast concrete elements can be constructed in one of Thomas Betong’s precast concrete plants. Thomas Betong has plants in Lane-Ryr, Sollebrunn, and Heby. In November, I worked in the Sollebrunn plant for two weeks. In Sollebrunn, they construct a wide variety of products such as sandwich walls, walls, prestressed slabs, balconies, pillars, beams, and slabs. During the period in Sollebrunn I got the opportunity to join all teams and try out to build all sorts of elements. I had no experience with prefab construction prior to the period, but the team was very helpful and explained all the different steps and processes. Something that particularly impressed me was the great freedom in façade design with the sandwich walls. In Sollebrunn, they produce sandwich walls with bricks, which I found very beautiful!
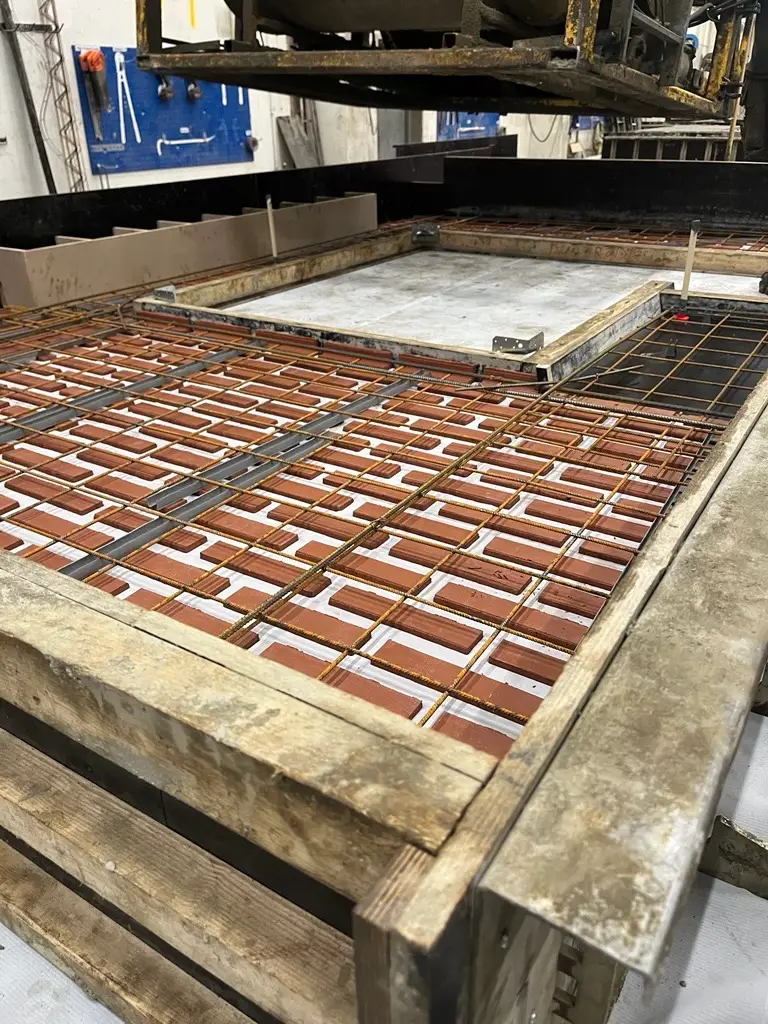
At the turn of March/April, I and Clara spent two weeks in Heby where Thomas Betong has two plants. In one of the plants, they produce filigree floor slabs, balconies, and half sandwich walls, Heby 1. In the other plant they produce double walls, Heby 2. The first week I worked in Heby 1 and I joined Burzo Kurdu Bakir’s team. I had the opportunity to build balconies and filigree form slabs. Everyone in the teams was very helpful and explained how and why the elements were built in a specific way.
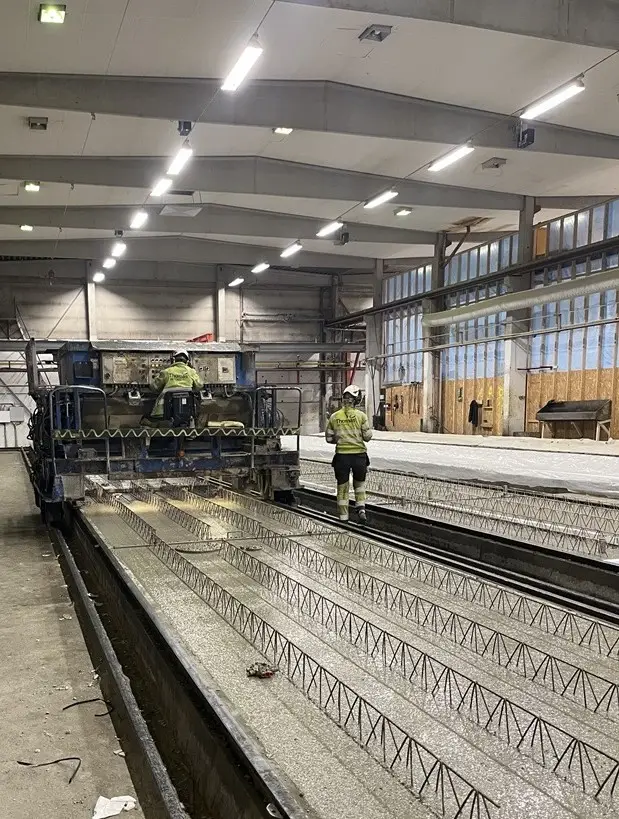
During the second week, I worked in Heby 2, where double walls are produced. Heby 2 is a very modern precast concrete plant with form tables moving around the facility and a robot assisting in marking out the dimensions of the walls, any embedded items, etc. The modern plant allows for industrial production at a high rate. During the week, I worked with Emanuel Edberg’s team and had the opportunity to try out different workstations in the plant. The team was very kind and explained the steps and why they built the elements in a specific way to allow for the high-paced production of double wall elements. Before I started at Thomas, I didn’t know what filigree floor slabs and double walls were. Therefore, it was fun to get hands-on experience with the elements.
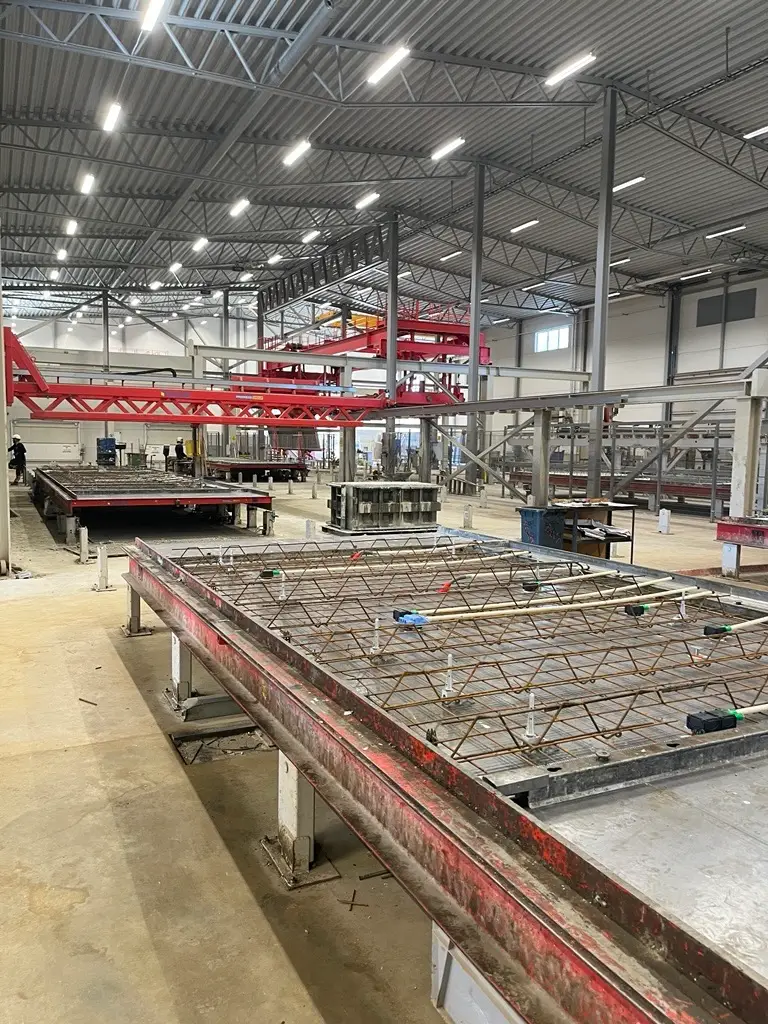
Once the precast concrete elements are constructed, they are ready to be sent to the project for assembly. The elements are sent at the requested time from the customer and according to the project manager’s delivery plan. When I was in Stockholm, I had the opportunity to participate in a site visit on a project to which Thomas Betong delivers several different types of elements, such as sandwich walls, filigree floor slabs, double walls, and balconies. During the site visit, double walls were delivered and assembled on-site.
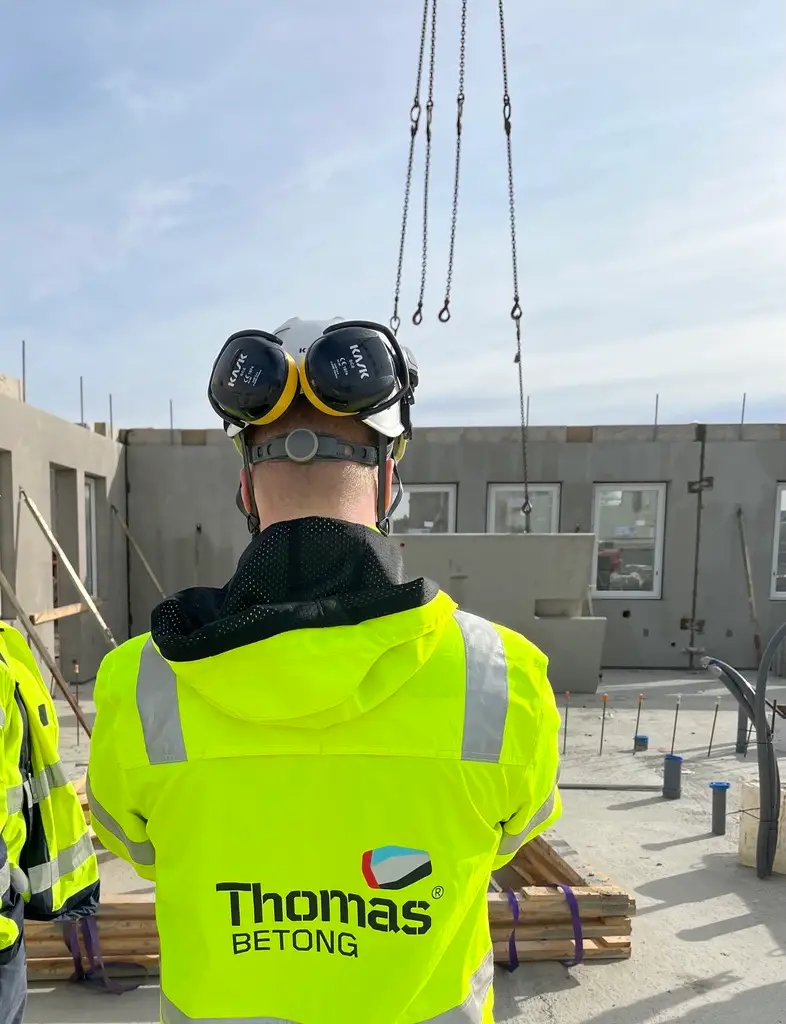
This was my longest blog post so far, and I would be impressed if you managed to read all the way through. It has been very enriching to see the entire process from quotation to assembly of concrete elements. One key takeaway for me is the importance of communication and coordination between the different stages to deliver according to the agreement with the customer and ensure their satisfaction. The next period will be at the finance department on Södra Vägen. Stay tuned!