Karlatornet is not just the tallest building in the Nordics. With its 73 floors and 246 meters, it is also one of the tallest residential buildings in Europe. The building was designed by Skidmore, Owings and Merrill, who were also the architects behind One World Trade Center in New York.
“The slenderness of the building is reminiscent of some of the world’s most iconic skyscrapers, such as the Burj Khalifa. To ensure stability so that living comfort is not affected, we have built in outriggers that function as stabilizers. Just as poles help a skier maintain balance, the outriggers prevent the tower from swaying in strong winds,” explains Jörgen Österlund, project manager for Karlatornet at the construction company.
Innovative concrete technology behind Scandinavia's tallest building
Many tests and test casts were carried out before the 246-meter-high Karlatornet tower was completed as a new landmark for Gothenburg, to which Thomas Betong delivered 62 000 m3 of concrete.
The wide piles, 50–70 meters deep and 2 meters in diameter, on which the entire building rests, required a concrete mix with exceptional properties. It was estimated that casting would take about 9 hours and take place through a cast pipe. Therefore, the concrete needed to be able to flow out and be compacted for up to 12 hours, without releasing water, despite the high pressure at the bottom. This required a self-compacting concrete with an extra-long opening and low water bleeding.
“Through advanced tests with the special Bauer Concrete Filter Press, we were able to ensure the quality and properties of the concrete,” says Ingemar Löfgren, R&D Director at Thomas Concrete Group.
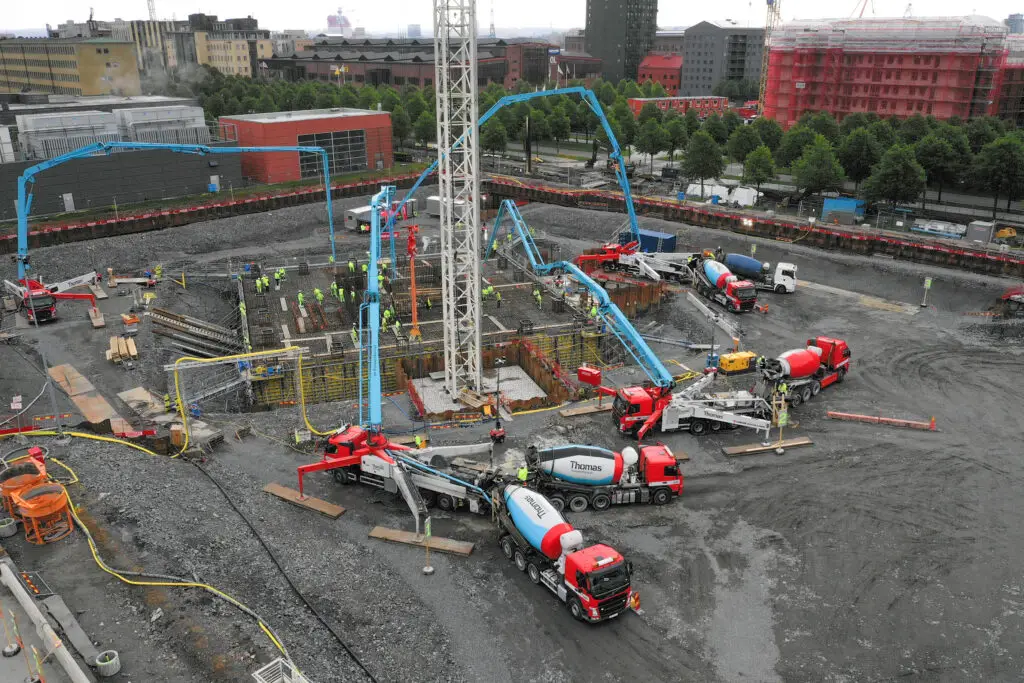
High-strength concrete was used for the core and pillars themselves, where durability and rigidity were crucial.
“We replaced parts of the cement with slag and used microsilica, which improved the pumpability and strength of the concrete and facilitated the construction process. But pumping the high-strength concrete was a challenge, and the pump had to be located a good distance from the core due to lack of space, which did not make things any easier,” says Ingemar Löfgren.
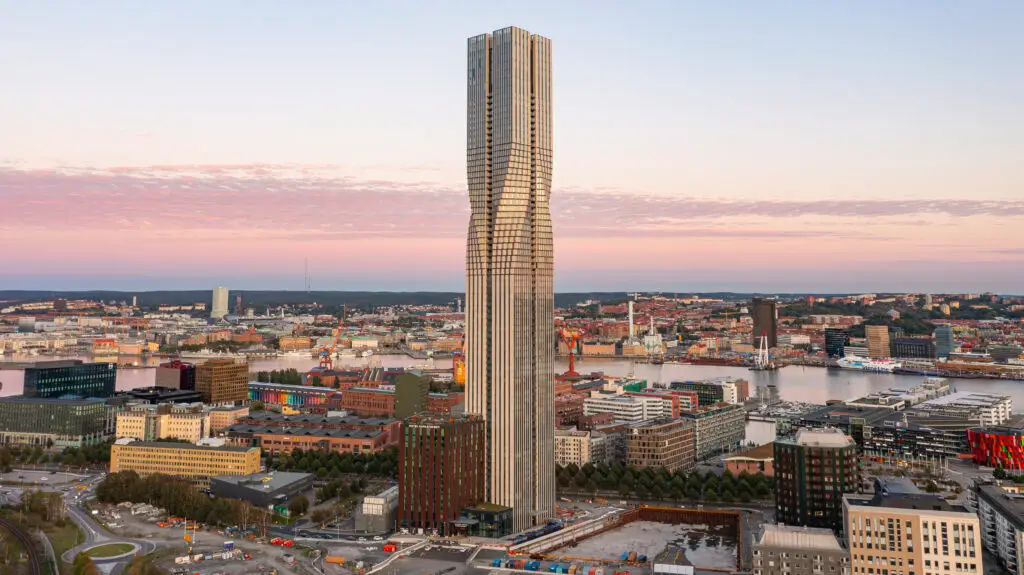
A journey of innovation and collaboration
The outrigger walls, which connect the core and the columns, required a self-compacting concrete with high strength and small aggregate size. For the floors, which are post-tensioned to reduce thickness, a careful adaptation of the concrete was needed to meet requirements for compressive strength and temperature development under different conditions.
By using over 30 different concrete mix designs adapted to different seasons and weather conditions, Thomas Betong was able to ensure the stability and progress of the structure. The project, which ran from the Fall of 2016 to November 2023, has been a journey of innovation and collaboration.
“Sampling and test castings have been very valuable and have saved time and reduced the risk of errors, while dialogue and learning during the project have been indispensable. Together, we have succeeded in creating a sustainable structure that will be an icon for Sweden for many years to come. I am really proud of the commitment that everyone involved has shown,” concludes Ingemar Löfgren.
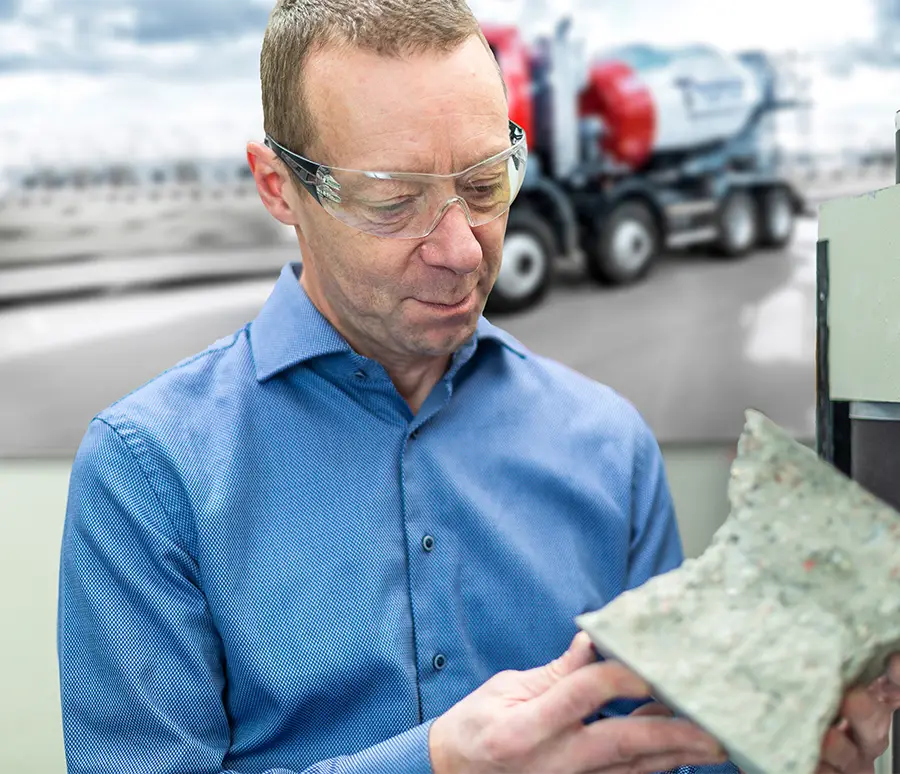